Make it easy for people to reduce at risk working
- Allison Reynolds
- Nov 15, 2018
- 3 min read
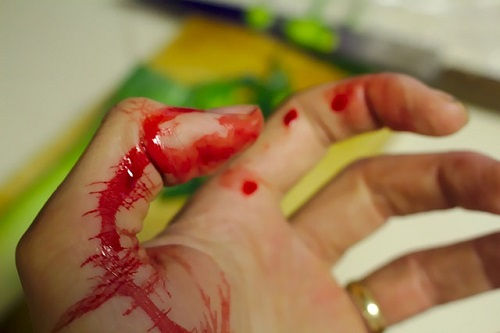
One of the things that makes our behavioural programmes so impactful is that that they facilitate action learning. Participants stop and reflect on real life problems that are happening around them. We give people a simple behavioural framework to analyse their problems against, create the environment whereby they engage in the process and then sit back and watch the pennies start to drop.
This is one of my favourite stories from 2018 about just that.
A construction team had experienced a problem on site when an operative nearly lost a finger cleaning his mixing tool. The operative had kept his hand in a bucket of water to clean the blades whilst gently pressing the operating switch on the tool with the other hand to rotate to blade. He pressed too hard on the switch and had a bad injury.
The safety management team initially did what safety management teams often do, they sent out a red safety alert, they look into banning the tool, they spoke to every man and his dog but as usual this had little impact on day to day behaviour. And then everyone moved onto the next issue.
A couple of months later the team participated in a behavioural leadership programme. As part of the programme delegates were asked to reflect on a recent incident and analyse it using the tools provided.
Dr Ryan Olson, a Scientist at Oregon Institute of Occupational Health Sciences developed the Performance Equation to help understand and evaluate employee and individual performance. The Performance Equation is a simple, memorable but very effective tool for identifying, prioritising and addressing gaps in the current work environment:
PERFORMANCE = (ABILITY + MOTIVATION) – OBSTACLES
On reflection the team found that they’d got their initial investigation and resulting interventions wrong. They hadn't identified what triggered the behaviour. They hadn’t identified what reduced risk behaviour they’d have wanted the operative to do instead. They hadn't looked at the environment at all.
Using the performance equation they identified an obvious obstacle. The operative had no practical, available option to be able to clean his tool. And his at risk behaviour was reinforced because he had repeatedly cleaned his tool this way for years and never had an injury.
After discussion with the workforce they are now looking at purchasing cleaning buckets for all operatives that use mixing tools. The cleaning buckets have a lid that you can place the mixing blades through and have brushes inside. The buckets can receive water and when you place the blade inside and switch on the tool the brushes clean the blades and therefore keep the operatives hands away from the rotating tool. Simple, clean, practical easy , to make available and use.
What I love about this story is the simplicity, the operative had no practical, available option to be able to clean his tool, why would we expect anything else?
What I love even more about this story is the learning. Once you understand the impact of environment on behaviour, you can’t unlearn it. This one small change, a team shifting their focus from doing what they’ve always done, to asking the question, what will make this behaviour less likely and the desired behaviour more likely, from the operatives perspective, is hugely powerful.
Now imagine all of the supervisors, managers and support team in the business problem solving in this way.
Sustainable change rather than constantly revisiting the same issues over and over.
allison@sciencebasedleadership.co.uk
Comentarios